How to prepare for an ISO 17025 audit as a small lab
Preparing for an ISO 17025 audit is always a challenge, requiring significant time and effort. The time and dedication required from staff when you are a smaller lab can also make this whole process an even more challenging one. When “all hands on deck” isn’t all that many pairs of hands, there is no doubt that being a smaller lab presents a very different challenge to larger laboratories. At Ideagen, we have worked with labs with as few as 8 members of staff, so when audits are on the horizon, it pays to be prepared.
Read on for our tips for how to make sure you are always audit ready and how you can leverage QMS software, even as a small lab, to make sure you are never caught out when it comes to your next audit.
One great way to ensure that you are always audit ready is to have an established calendar of internal audits. Watch our webinar on auditing skills today and make sure you’re never caught out again.
Watch the auditing masterclass
Join Melanie Ross for a masterclass on key skills for carrying out audits.
Watch nowA small lab case study
In another recent webinar, we heard from Michelle Robertson on how she prepared her small lab for ISO 17025 audits. When Michelle began her role as the Quality Assurance Officer at the Guadalupe-Blanco River Authority (GBRA), she faced a daunting task. GBRA's documentation consisted of over 700 hard copies and more than 260 bench sheets - an overwhelming volume by any standard. But you read that right: these documents were still paper based, making the retrievability of documents difficult and time consuming.
Handling these documents was complicated due to their chaotic arrangement, managed through a mix of shared drives, manuals, binders, an outdated electronic archive system, and two overflowing file cabinets located separately. This state of disorder was far from ideal for audit readiness.
Adding to the disorderly document management system, Michelle had to combat the issues caused by staff turnover. With a shortage of manpower, information flow and tracking suffered. To further worsen the situation, updates to the Standard Operating Procedures (SOPs) weren't happening promptly, causing additional challenges for the staff. Additionally, there were several problems related to equipment and software.
These challenges are common in a small lab setting, but how can you make sure you are still prepared for ISO 17025 audits?
What are the key elements to unlocking audit readiness?
To be audit ready, there are some key points you need to have strong, efficient processes for. As a small lab, you will need:
- A way to keep documents in one place and, crucially, ensure they are easily retrievable. Having them in a filing room is all well and good, but if locating certain documents is a time-consuming task in itself, you will be taken away from more important lab duties.
- Have robust processes for managing proficiency tests and lab training. Track employee training progress and performance.
- Establish and roll out effective processes for SOPs, CARs, workflows and all other processes. Having all parties in your quality system working to the same processes will greatly increase your audit readiness.
- Establish procedures for personnel change management. This should go hand in hand with your efforts to establish robust proficiency testing and lab training, but it is also important to have similarly well-established processes for bringing new starters up to speed – or bringing existing staff up to speed in a new role – as quickly as possible.
- A way to keep documents up to date and approved by relevant parties. Being able to track revisions, have them signed off, and easily accessible, are all the hallmarks of audit readiness.
- Set up procedures for managing complaints and feedback. There are few better ways to learn what is or isn’t working for your lab, and such feedback can be crucial for avoiding non-conformances when your next audit comes around.
- Set up automated workflows for key procedures. You can be extra confident that key processes are being carried out accurately and effectively, such as equipment calibration and testing, by implementing automated workflows. Know exactly what actions need to be taken and when.
- Carry out internal audits. The internal audit is essential for upholding quality. Watch our webinar on key internal auditing skills now to learn more.
The results of implementing the above
If you put into practice the above measures, we know from Michelle at GBRA and many other of our customers that:
- You will have better continuity in the face of staff turnover
- Greater staff accountability for the whole quality system and especially for the documents within it
- No more “uncontrolled” documents floating around
- No more (or greatly reduced) publication errors when submitting revisions or new documents
- Documents are easily retrievable, saving time and making them easy to prepare for audits
- Fewer errors and mistakes as workflows govern the testing of key equipment
- Error rates greatly reduced in all other areas too, and responsibility and accountability rests with employees
Why Ideagen Quality Management?
There is a misconception that you have to be a large organization to use quality management software like Ideagen QMS, but actually our customer base really varies in size. We have many users who are from organizations as small as 25-50 people, and Michelle at GBRA found herself in a team of just 8 while greatly benefitting from using Ideagen Quality Management.
In order to handle audits more effectively, Michelle Robertson and her team decided to implement a Quality Management System (QMS). The implementation of Ideagen Quality Management (formerly Ideagen QMS) began in May 2018 and was completed by October 2019, with the whole team properly trained by then.
This decision yielded many benefits for the lab. For example, it improved the efficiency of their quality management efforts, automated essential processes, reduced mistakes and fostered a sense of responsibility among the team members.
The move to a centralized eQMS was an essential development for the Guadalupe-Blanco River Authority (GBRA). By making the transition, it enabled better control over their documents and improved their audit readiness. It provided them with new capabilities that allowed them to manage their data more efficiently and make sure they were compliant with ISO 17025 standards.
Interested in implementing powerful eQMS software in your small lab setting? Learn more about Ideagen Quality Management today and book a conversation with our team about how it could be the right solution for you.
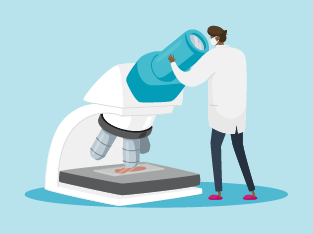
How can Ideagen Quality Management benefit you?
Discover how Ideagen Quality Management can benefit your small lab and increase your audit readiness.
Learn moreTags: