JAE Oregon maintain ISO certification and reduce document approval times to just 48 hours
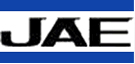
Based on the west coast of the US, JAE Oregon is a world-class manufacturer of technologically advanced, high-quality connectors.
JAE’s connectors – which are made in Tualatin, Oregon, and in Tijuana, Mexico – are shipped throughout the world for use in a variety of automotive applications from airbag systems to iPad connections.
JAE Oregon’s parent company is Japan Aviation Electronics (JAE), Ltd., which has several subsidiary manufacturing facilities worldwide. JAE Oregon is the only one located in the US, and the company primarily serves the US domestic and European markets.
The challenge
The company had previously been using a system to manage their compliance issues which had been developed “in-house” from various offthe- shelf software packages.
Scott Bayha, Quality Manager at JAE Oregon, said: “We had been working with in-house developed disparate systems and they were failing to keep up with our demands.
We were experiencing a number of issues – such as the security and retrieval of data – and there was a lack of communication with the QMS as well as the issue that none of our various systems were linked to each other.”
The challenge
The company had previously been using a system to manage their compliance issues which had been developed “in-house” from various offthe- shelf software packages.
Scott Bayha, Quality Manager at JAE Oregon, said: “We had been working with in-house developed disparate systems and they were failing to keep up with our demands.
We were experiencing a number of issues – such as the security and retrieval of data – and there was a lack of communication with the QMS as well as the issue that none of our various systems were linked to each other.”
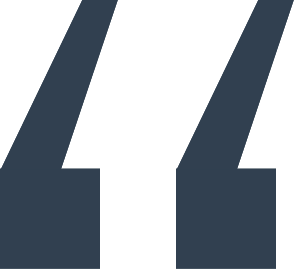
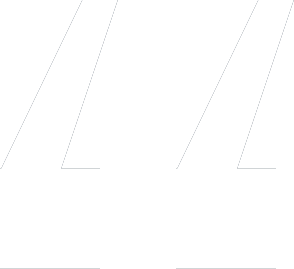
We have reduced the average document approval time from draft to approval from almost two weeks to less than 48 hours.
How did Quality Management help JAE Oregon maintain certification to ISO 9001 & 14001?
Quality Management was chosen to replace the in-house system, making it easier to maintain certification with both the ISO 9001 and ISO 14001 standards.
Scott added: “We found out about Quality Management after it was recommended by a similar organization within the manufacturing industry, and immediately recognized a number of notable benefits it would bring to the business.
“The single biggest impact that Quality Management had on our company was within document management.
We’ve reduced document revision, review, approval and publishing from nearly a two-week process to about 48 hours
“The single biggest impact that Quality Management had on our company was within document management. We’ve reduced document revision, review, approval and publishing from nearly a two-week process to about 48 hours
Quality Management's Document module – alongside its ability to automatically communicate with us, providing instant, automatic messaging – provided excellent revision control, ensuring that the correct document revision is
being accessed.
“The review and approval process within Quality Management is outstanding and means we can see exactly who is reviewing each document and if they have any comments in regards to it.
The fact that Quality Management automatically notifies us of any changes within the management system via email is very beneficial.
It tells you what is happening and when it is happening, making the steps in the process easy to follow. For us, this was an outstanding feature.”

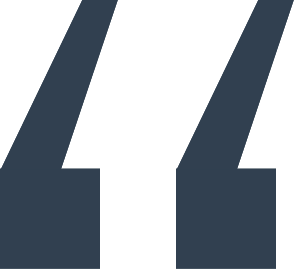
We realized that just use of the Document module would justify the entire Quality Management system and over time that has indeed been the case.
Benefits
Document revision times reduced from two weeks to just 48 hours
Automatic email notifications inform management of what is happening and when
Increased participation with the QMS means staff feel a “sense of ownership”
“Extraordinary” customer service and support provided by Ideagen’s partner Process Power Solutions Inc
JAE Oregon’s commitment to product quality and customer satisfaction provides a strong competitive advantage in an expanding global industry.
Through Quality Management, the company’s mission in providing high quality, cost effective electrical components and services have been accomplished through state-of-the-art quality processes, on-time delivery and an aggressive continuous improvement philosophy.
Scott added: “The functionality of the Document and CA/PA modules has assisted us in increasing our overall proficiency as a company and the success of the solution has led to some of our users looking for and suggesting additional uses for Quality Management, including implementation at our Tijuana branch.
Some users have requested expanded permissions so they can use the tool more intensely.
Increased participation in the quality management system pays dividends in more ways than just having correct document revisions on the floor.
It means everyone feels a sense of ownership in a system that was formerly perceived to be the “responsibility” of a small group.
“On selecting Quality Management, we used a cost justification spreadsheet to assist in the decision making process.
From this, we realized that use of just the Document module would pay for the entire Quality Management system and over time this has indeed been the case. The software has been everything we hoped for.
What we had not anticipated was the extraordinary customer service and support we received from our Quality Management provider, Ideagen’s partner Process Power Solutions, Inc.
Their help in planning, implementation, training, and ongoing support have been invaluable. So we are very happy with the Quality Management product.”
Find out how Ideagen’s Quality Management system can help improve your quality and audits
Contact us to find out how you could introduce streamlined and centralized control within your organization.
Find out more
Find out how Ideagen Quality Management has helped even more of our customers
Tags: