Tecomet reduces production part approval process by 80%
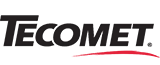
Founded in 1963, Tecomet is the market leading provider of manufacturing solutions for complex, high precision products and services for the Medical Device and Aerospace & Defence markets.
Tecomet operates 16 global manufacturing facilities in five countries around the world and employs over 2,500 staff.
Medical device maker, Tecomet, approached Ideagen to discuss their products and consultancy services in a bid to improve its New Product Introduction (NPI) process and Production Part Approval Process (PPAP).
Together, Ideagen and Tecomot discussed the services Ideagen could offer, including the benefits of implementing Ideagen’s suite of applications that would help manage the company’s quality inspection and process management tasks involved in new product introduction.
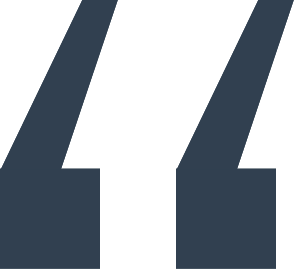
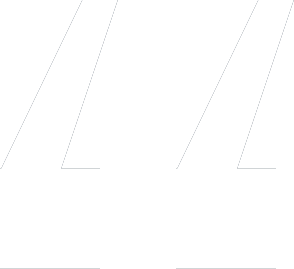
For the first time, we now have a PPAP ready before we’ve finished making the part - and that’s something that has never happened before.
Carl Andrews, the Account Manager at Ideagen who worked closely with Tecomet said: “After speaking with the team at Tecomet, it was clear that Quality Control was the ideal software solutions to bring their operations into the modern day. By that, I mean replace their previous manual processes with new, modern and digital versions.
Quality Control would streamline the entire PPAP management process, allowing Tecomet to electronically prove that their manufacturing processes consistently met design requirements during an actual production run.
“At the same time, Quality Control offered them a customizable workflow to establish and manage a gated process for new parts and assemblies – a simple but powerful process management tool that helps reduce risk.”
Sallyanne Lowe, Tecomet’s Program Manager, said: “Previously, a PPAP for our customer took a total of three days and involved paper being laid out everywhere across tables.
With Quality Control , I can now do a PPAP with similar requirements in just a few hours.”
Carl Andrews, the Account Manager at Ideagen who worked closely with Tecomet said: “After speaking with the team at Tecomet, it was clear that Quality Control was the ideal software solutions to bring their operations into the modern day. By that, I mean replace their previous manual processes with new, modern and digital versions.
Quality Control would streamline the entire PPAP management process, allowing Tecomet to electronically prove that their manufacturing processes consistently met design requirements during an actual production run.
“At the same time, Quality Control offered them a customizable workflow to establish and manage a gated process for new parts and assemblies – a simple but powerful process management tool that helps reduce risk.”
Sallyanne Lowe, Tecomet’s Program Manager, said: “Previously, a PPAP for our customer took a total of three days and involved paper being laid out everywhere across tables.
With Quality Control , I can now do a PPAP with similar requirements in just a few hours.”

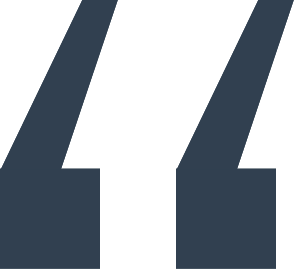
Previously, a PPAP for our customer took a total of three days and involved paper being laid out everywhere across tables. With Quality Control, I can now do a PPAP with similar requirements in just a few hours.
How did Quality Control reduce production part approval process by 80% at Tecomet?
Sallyanne continued: “Because of the way the software is laid out, the elements and requirements are logical and gives us confidence in the quality of the packs content we submit – whether it’s a PPAP or NPI.
“The structure of the software forces you down the correct route for filling in forms. So, should a colleague be off, it’s very easy to pick up where they are and continue with the work.” Sallyanne added: “For the first time, we now have a PPAP ready before we’ve finished making the part – and that’s something that has never happened before.”
Carl added: “Quality Control added valuable functionality for the manufacturing industry.
Within that industry, organizations such as Tecomet are under pressure to compress lead times while maintaining quality and improving consistency.
“Quality Control is a powerful project management tool as well as a quality management tool. Engineering, quality, production and other departments will all be involved in the PPAP or NPI process at some stage.
With so many interconnected elements, it’s important to manage the process efficiently and maintain visibility.”
Benefits
Modern, electronic processes reduce the need for substantial amounts of paper
Risks associated with possible variation are removed thanks to electronic workflows
Important and complex tasks are electronically and automatically mistake proofed
PPAP process reduced from three days to a few hours
Smooth PPAP process ensures PPAPs are completed before the part is made Q-Pulse PPAP helps Tecomet reduce production part approval process by 80%
Could Quality Control become your gateway to improved quality management?
Contact us to find out how you could introduce streamlined and centralized control within your organization.
Could you benefit from reducing your PPAP process by 80%?
Find out how Quality Control has helped even more of our customers
Tags: